De plus en plus souvent confrontés à des restrictions de prélèvement, les industriels se tournent vers des ressources non conventionnelles pour produire leurs eaux de process. Ce qui implique des traitements plus onéreux et plus complexes à opérer. Mais ont-ils encore le choix Pour répondre à la demande, les traiteurs d’eau peaufinent leurs technologies et adaptent jusqu’à leur business model.
Grands consommateurs d’eau pour leur process, les industriels ne peuvent en général pas se contenter d’eau brute. Selon les branches, et même selon l’étape de leur procédé, il leur faudra la traiter pour arriver à une eau déminéralisée, potable, voire ultra pure… Ils recherchent évidemment pour cela les solutions les moins onéreuses. En termes de ressources tout d’abord, ils privilégient les eaux de forage, relativement «propres» et ne revenant qu’à quelques centimes au m3 avec un traitement léger, plutôt que l’eau de ville, certes potabilisée mais beaucoup plus onéreuse et demandant en général un traitement de finition. En matière de technologie de traitement ensuite: outre l’investissement initial, ils seront attentifs au coût opérationnel et aux compétences nécessaires pour faire fonctionner les installations. L’histoire pourrait s’arrêter là mais l’évolution climatique, avec son cortège de restrictions et d’«arrêtés sécheresse», change la donne.
Confronté au risque de fermeture d’une usine, ou tout au moins d’une diminution importante de sa production, l’industriel doit pouvoir se tourner vers des ressources alternatives, généralement de moins bonne qualité qu’initialement: eau pluviale, eau de surface, eau recyclée, eau usée traitée… Évidemment, cela va impliquer des traitements plus poussés donc plus onéreux et plus complexes à opérer pour amener ces eaux à la qualité requise. C’est là qu’interviennent des traiteurs d’eau généralistes comme Veolia Water Technologies ou Saur (via sa filiale Nijhuis Saur Industries), ou plus spécialisés comme John Cockerill, Waterleau, Atlantique Industrie, BWT, Babcock Wanson, Chemdoc Water Technologies, Afig’eo, Aquaprox I-Tech, Lenntech, Nereus ou Elmatec, entre autres. Certains maîtrisent une technologie particulière (membranes, résines, UV, fibres polymères, évapoconcentration …), à l’instar de Polymem, NX Filtration, Bio-UV Group, UV-Germi, Ajelis, Hydrobios, Greenlife, Acqua.ecologie ou TMW.
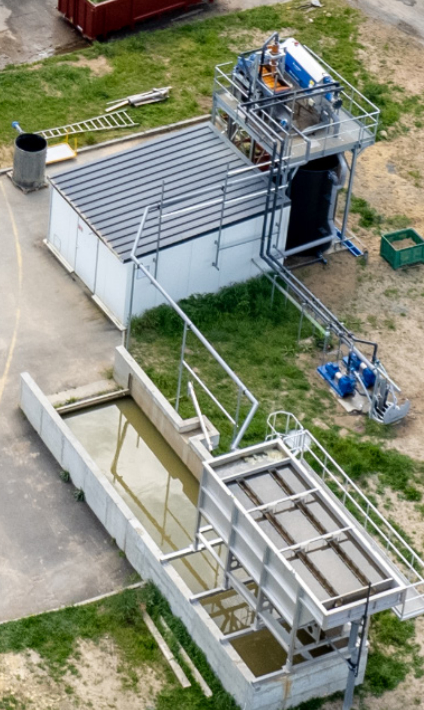
D’autres encore, chimistes à
l’origine puisqu’il faut souvent des réactifs pour traiter l’eau, en sont venus à
concevoir et proposer des solutions
complètes de traitement, comme Nalco
Water (groupe Ecolab) ou Adiquimica.
Par ailleurs, en matière de stockage il
existe de nombreuses solutions dont les réservoirs boulonnés qui apportent une
grande flexibilité en termes de dimensions, de mise en œuvre, d’équipements
et une grande facilité de maintenance/
nettoyage. Ils constituent une solution
technico-économique largement utilisée par les industriels pour le stockage
des eaux de REUT, de process, avant et
après traitement.
«Le traitement d’eaux non conventionnelles a certes un coût mais l’industriel joue la pérennité de son activité. Il
est donc souvent prêt à mettre le prix,
tout au moins en termes d’investissement. Il sera cependant très attentif aux
coûts d’exploitation, à l’OPEX, car toutes
ces technologies de traitement poussées
consomment un peu plus d’énergie ou
de réactifs que ce qu’il utilisait auparavant» explique Nabil Mabrouk, Directeur
commercial chez John Cockerill. Moins
optimiste, Stéphane Laporte, Sales and
Business Development Manager chez
Nijhuis Mobile Water Solutions, tempère: «d’après mon expérience, le temps
de retour sur investissement pour une installation de recyclage d’eau est de l’ordre
de dix ans, or les industriels privilégient
des temps de retour beaucoup plus courts.
Hormis certains qui le font pour des raisons d’image de marque, ils ne se lanceront
dans le recyclage que s’ils y sont obligés.»
FRANCHIR LE PAS
Une obligation qui semble bien se profiler… Restrictions aidant, les industriels doivent désormais franchir le pas, ou tout au moins s’y préparer. Investissement, Opex, personnel qualifié: il faudra en passer par là pour continuer à produire. Toutefois, avant même de se lancer dans le recyclage des eaux de process, voire la réutilisation des eaux usées, la première étape consiste évidemment à économiser l’eau dans le procédé. «Depuis les arrêtés sécheresse des années 2022-23, nous sentons une vraie volonté des industriels d’aller vers les économies en général. La majorité a passé l’étape nécessaire de la connaissance et la maîtrise des flux dans l’usine, et utilise la démarche dite 3R (réduire, réutiliser, recycler). Cela commence par l’amélioration des procédés, par exemple l’optimisation du nettoyage en place» affirme ainsi Mikael Tournaux, Responsable du marché agroalimentaire à la Direction commerciale industrie de BWT.
Nalco Waters propose ce type de démarche. «Nous proposons d’abord un audit complet au niveau du site pour identifier la meilleure approche et la meilleure solution pour le client. Cela ne passe pas nécessairement d’emblée par du recyclage : nous apportons aussi des solutions d’optimisation des consommations d’eau, de réutilisation, etc.» explique ainsi Patrice Hervé, Senior Marketing Manager chez Nalco Water. Chemdoc Water Technologies prône une approche similaire. «Avant d’envisager la REUT, il est essentiel de réaliser un audit de l’usine. Cartographier les usages, les ressources disponibles, les qualités exigées, les équipements déjà en place… C’est une procédure que nous avons calibrée, et que nous appelons le 360-4R, pour évaluer tout ce qu’on peut réduire, remplacer, réutiliser…» détaille Salvador Pérez, Directeur de Chemdoc Water Technologies.
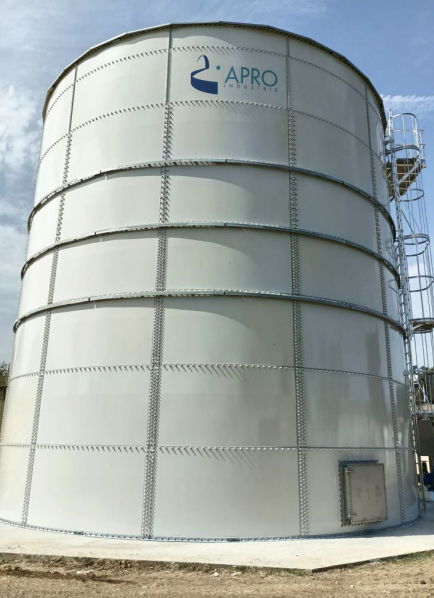
Odyssée Environnement accompagne les entreprises dans toutes les étapes de ce processus d’évaluation des besoins, de réduction des consommations et de surveillance continue des flux. Sarpi ThinkTech propose des solutions complètes de traitement des eaux, impliquant en premier lieu un diagnostic (cartographie des flux et des besoins du process), puis le choix de la filière la plus appropriée, des tests en laboratoire et/ou pilotes et enfin la fourniture de la solution. A cela s’ajoutent au besoin, l’exploitation et la maintenance. L’optimisation de la consommation a cependant ses limites. En cas de restriction sur les prélèvements, il faut bien envisager le recyclage. Le terme recouvre en fait différentes réalités. Cascade d’une étape du procédé à une autre moins exigeante en termes de qualité ou réutilisation en boucle courte après un traitement léger n’impliqueront pas les mêmes investissements que la réutilisation des eaux usées traitées (REUT) en sortie de STEU.
«Nous proposons en premier lieu de recycler de
l’eau dans le process, avec des équipements simples. C’est beaucoup moins
onéreux que de mettre en place une
REUT, qui suppose souvent des budgets
de plusieurs centaines de milliers d’euros. C’est la démarche que nous avons
proposée, par exemple, à L’Oréal ou
Sarbec, des cosméticiens. En installant
un traitement simple de leurs concentrats
d’osmose, on fait économiser 5% d’eau
sur la consommation globale du site avec
un investissement modéré» avance ainsi
Dimitri Monot, Responsable de l’Activité REUSE chez BWT. «A contrario, la
valeur ajoutée du traiteur d’eau que nous
sommes se concrétise plutôt au niveau
de la REUT, car le recyclage à l’intérieur
du procédé peut être géré par l’industriel lui-même. L’enjeu de demain est bien
la dernière brique : la REUT» souligne
cependant Mikael Tournaux (BWT).
En pratique, l’équation se présente
différemment selon les branches
industrielles.
AGROALIMENTAIRE :
UN CAS À PART
L’industrie agroalimentaire constitue un cas particulier. Tout d’abord à cause des exigences réglementaire élevées, basées sur d’évidentes raisons sanitaires, quand à la qualité de l’eau amenée à entrer en contact avec les aliments, voire à les constituer. En France, le recyclage (et à plus forte raison la REUT) ont jusqu’à très récemment été interdits dans ce secteur. A cela s’ajoutent des exigences «internes» propres aux industriels : labels, certifications internationales, etc. «L’univers agroalimentaire est très strict et régi par différentes exigences de qualité. Pour proposer des solutions de recyclage ou de REUT dans ce secteur, il faut être en mesure de tout démontrer, de s’insérer dans le plan qualité de l’industriel» souligne ainsi Salvador Pérez (Chemdoc). Autre particularité de ce secteur : malgré leur consommation élevée, en particulier pour les nettoyages en place, certains procédés sont globalement excédentaires en eau. C’est le cas en particulier dans l’industrie laitière, qui génère de grandes quantités d’eaux de concentration de matières laitières (ECML), de qualité déjà très élevée. Les sucreries ne sont pas en reste, avec le produit de l’évaporation des jus (de betterave ou de canne), lui aussi d’excellente qualité.
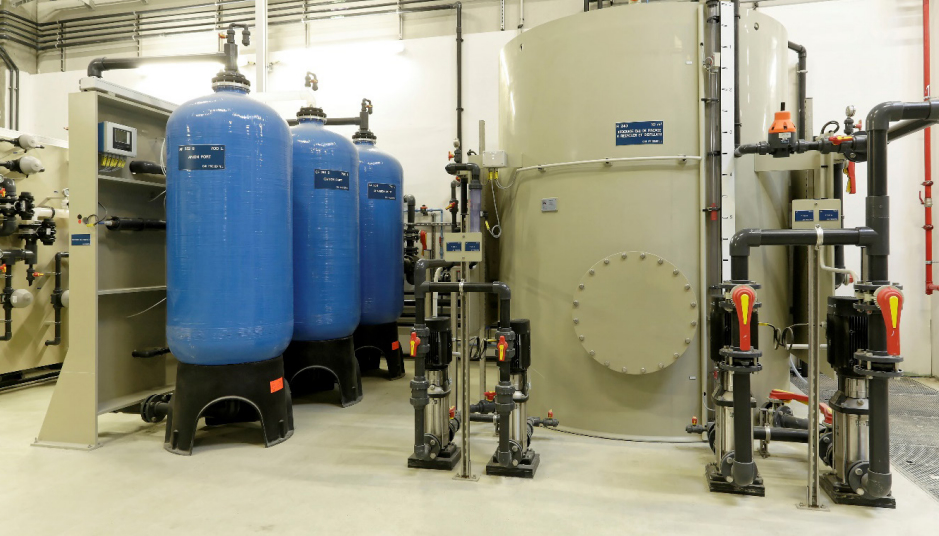
Autant d’eaux qui jusqu’à présent ne pouvaient pas être réutilisées dans le process et, généralement, partaient en STEU. C’est donc peu dire que le décret du 24 janvier 2024 «relatif aux eaux réutilisées dans les entreprises du secteur alimentaire» était attendu… La porte est enfin ouverte au recyclage et à la REUT pour les nettoyages en place mais pas pour faire de l’eau ingrédient toutefois. «Nous attendons l’arrêté d’application. C’est lui qui précisera comment recycler l’eau, quelle est la qualité attendue pour chaque usage, sous quelle modalité, avec quel contrôle HACCP. Il faudra écrire ça noir sur blanc pour sortir de ce flou artistique» expose Mikaël Tournaux (BWT). Une première mouture de ce texte ayant suscité une levée de boucliers de la part des industriels du secteur, le gouvernement revoit actuellement sa copie. A l’heure où nous mettons sous presse, la nouvelle version est encore en discussion au niveau des ministères. «C’est essentiel. Cet arrêté va définir les sources autorisées, les usages, les qualités. Les industriels attendent aussi de savoir ce qui sera exigé en termes de moyens de contrôle, d’analyses… Techniquement, tout est possible, mais il faudra atteindre un équilibre technico-économique raisonnable. S’il faut mettre en place des filières de traitement de plusieurs millions d’euros pour répondre aux exigences du texte, rien ne se fera» prévient Patrice Hervé (Nalco).
Les technologies sont en tout cas déjà prêtes, la plupart étant déjà déployées pour produire de l’eau de process à partir d’eau brute (non recyclée), ou pour faire du recyclage dans d’autres secteurs. Pour la désinfection en entrée, Nalco utilise ainsi une technique spécifique: le dioxyde de chlore ultra pur. «Notre solution Naldiox ultrapur évite la présence de produits de dégradation comme les chlorates, très sévèrement réglementés, en particulier dans l’alimentation des bébés» explique Patrice Hervé. L’utilisation de chlore gazeux permet également de s’affranchir de la problématique des produits de dégradation (chlorites et chlorates) dans les eaux destinées à l’agroalimentaire. C’est un produit aujourd’hui sans mercure, sans chlorure, qui ne se dégrade pas au stockage. Pour les industriels souhaitant passer de la désinfection classique (à l’eau de Javel ou au dioxyde de chlore) au chlore gazeux, Eurochlore conçoit sur mesure des solutions complètes incluant le stockage des bouteilles de chlore, le matériel de soutirage, d’analyse et de régulation. «Cette solution tout-en-un permet une mise en place rapide et minimise le temps de mise en service. La manipulation est sécurisée, sans risque de projection et sans émanation» explique Matthieu Barreau, Business Manager chez Eurochlore.
Oxytrading mise pour sa part sur l’ozone pour désinfecter les eaux de process sans créer de sous-produits. En effet, l’ozone (O3 ) se retransforme rapidement, et spontanément, en dioxygène (O2 ). Les centrales d’ozonation de la société sont particulièrement adaptées au traitement en boucle de l’eau de nettoyage en place. Chemdoc produit également de l’eau de process, voire de l’eau ingrédient, pour des industriels de la boisson. «Les membranes prennent le dessus dans ce type d’application. La particularité du secteur est l’exigence d’hygiène, de nettoyabilité, donc nous réalisons en inox. Nous désinfectons les membranes avec notre procédé Catadiox, un générateur d’oxydant embarqué sur le système, qui fonctionne sans apport de produit chimique» précise Salvador Pérez (Chemdoc). BWT a pour sa part réalisé une installation de recyclage des ECML sur un important site laitier. Ces eaux, une fois traitées, sont dirigées vers la tour aéro-refroidissante (TAR), un usage pour lequel l’industriel utilisait auparavant de l’eau de ville.
Fleuron D’Anjou
et Ardo ont pour leur part fait appel à
Atlantique Industrie pour recycler les
eaux de lavage des fruits et légumes. Des
installations relativement simples, avec
tamisage, hydrocyclone-table vibrante
et décantation lamellaire (et toutes les
pompes nécessaires), suffisent pour
cet usage. La société espagnole Azud
intervient, entre autres, dans le secteur agroalimentaire en fournissant son
système de filtration à disques assistée
par air, Azud Helix Automatic AA, pour
le recyclage d’eaux de lavage des fruits,
légumes ou céréales. Une opération
indispensable dans une des régions les
plus arides d’Europe. Selon les besoins,
une filière complète comprend, outre la
filtration à disques, un affinage par ultrafiltration et une désinfection. Les eaux
traitées sont alors soit redirigées vers le
lavage des aliments, soit utilisée en TAR.
VERS LA REUT DANS L’INDUSTRIE ALIMENTAIRE ?
Le décret du 24 janvier concerne la réutilisation en général. Il convient cependant de distinguer la réutilisation d’eaux de process (ECML ou évaporats de l’industrie sucrière par exemple) de la REUT proprement dire, qui concerne les eaux issues de la STEU de l’industriel. Pour les premières, dites «Eaux recyclées issues des matières premières et eaux de processus recyclées», le texte instaure un simple régime de déclaration. La REUT, quant à elle, devra faite l’objet d’une demande d’autorisation, avec une clause inhabituelle puisque l’absence de réponse au bout de six mois vaudra refus. Or, comme l’affirme Salvador Pérez, de Chemdoc «tous les grands industriels du secteur ont des projets de REUT pour le nettoyage». Danone Pays-de-Bray a commencé à travailler il y a quatre ans sur le principe de la réutilisation (reuse). Un pilote d’ultrafiltration a été mis en place avec Nalco Water, et avec l’appui de l’Agence de l’eau. Il a permis de valider la faisabilité du process. Danone attend maintenant le décret d’application afin d’envisager sa mis en œuvre à l’échelle industrielle. Danone espère ainsi, dès 2025, réutiliser 200 millions de litres par an.
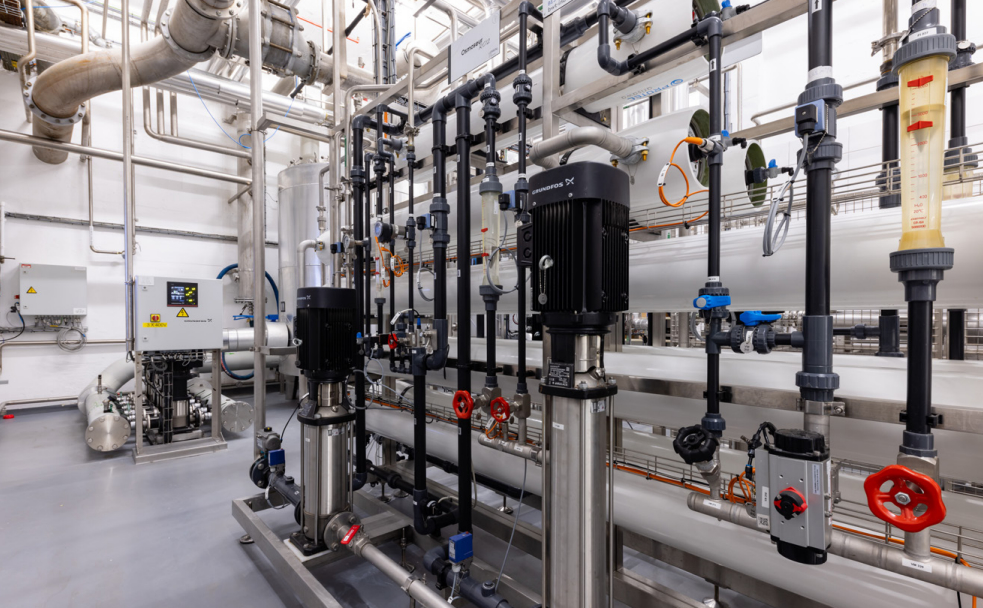
L’industriel espère ainsi réduire de 30% sa consommation d’eau. L’abattoir Bokail a fait un premier pas vers la REUT avec Atlantique Industrie, qui a d’ailleurs réalisé la STEU elle-même: une filière complète avec dégrillage/filtrage, aéroflottation, bassin d’aération, SBR et lagune de finissage. Une unité d’ultrafiltration conteneurisée, placée en sortie de lagune, permet de réutiliser de 3 à 5 m3 /j d’eau usée traitée. Dans le cadre de la REUT, il peut d’ailleurs être nécessaire d’améliorer les performances de la STEU de l’usine, en ajoutant des équipements ou en réalisant un traitement de finition. Qui plus est, pour les industries alimentaires, le projet d’arrêté ministériel précise clairement que les paramètres de potabilité définis dans l’annexe 2 de l’arrêté du 11/01/2007 doivent être étudiés pour qualifier les eaux brutes avant traitement complémentaire. Un grand nombre de ces paramètres ne sont généralement pas suivis en sortie de STEU, ce qui impliquera donc également d’ajouter des dispositifs d’analyse. IFB environnement suit et organise depuis 3 ans la faisabilité de projets de REUT pour des entreprises majeures de l’agroalimentaire en France. Cette faisabilité passe avant tout par un audit et un travail d’optimisation de la STEU de l’usine afin d’obtenir une qualité d’eaux brutes compatible avec leur potabilisation.
DES SECTEURS PLUS AVANCÉS
John Cockerill intervient historiquement dans le domaine du traitement de surface. Un domaine en général très avancé en matière de recyclage de l’eau, voire d’usines «zéro rejet liquide» (ZLD). «Le traitement de surface utilise depuis des années des eaux non conventionnelles. Etant donné la nature de leur effluents, chargés en métaux, les industriels étaient de toute façon obligés de les traiter avant de les rejeter. Ils se sont donc naturellement posé la question de la réutilisation de ces eaux traitées. On arrive à réutiliser ainsi 95% de l’eau usée, ce qui permet à la fois de pérenniser l’approvisionnement et de préserver l’environnement» explique Nabil Mabrouk (John Cockerill). La société a même développé une série standardisée de solutions basées sur une combinaison d’évapo-concentration et de traitement sur résines échangeuses d’ions : la gamme AcvaMod. «Nous avons d’abord déployé cette gamme sur les projets internes du groupe, pour les gigafactories en lien avec la production d’hydrogène. Et ensuite, auprès de nos clients» se souvient Nabil Mabrouk.
Des clients qui opèrent dans les domaines de l’aéronautique, la défense ou la microélectronique, que ce soit en France ou ailleurs en Europe. A l’instar de certains autres traiteurs d’eau, John Cockerill peut proposer un nouveau business model où l’investissement n’est plus supporté par le client mais par le fournisseur de l’installation de traitement. Ce dernier construit et exploite l’installation et se rémunère sur la vente du m3 d’eau de process, au travers d’un contrat de service de longue durée. Outre l’absence d’investissement initial, cela permet également à l’industriel de ne pas avoir à recruter et rémunérer les personnels formés à la conduite d’installations de traitement complexes. Nalco Water propose également ce type de contrat. C’est le cas, par exemple, auprès d’un important industriel de la chimie. «Nous avons construit une usine de production d’eau de process à partir d’eau brute et la lui vendons au m3 avec un engagement de production 24/24 car son usine ne peut pas s’arrêter. Cette eau entre dans la composition même de son produit, un additif pour l’industrie automobile» rapporte Patrice Hervé.
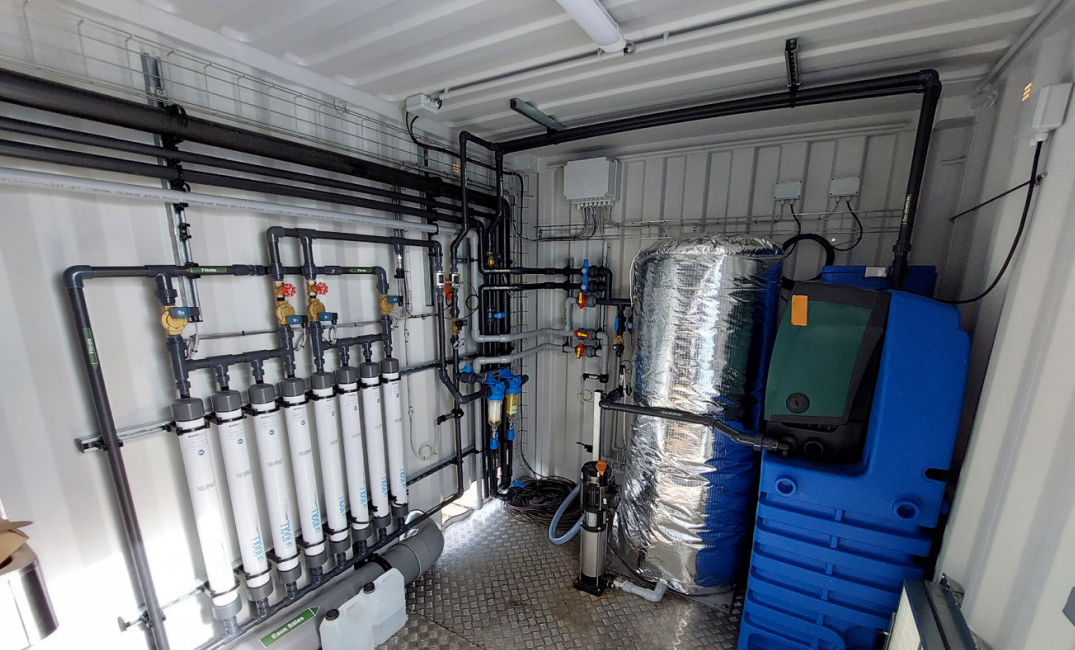
Nalco Water est également intervenu auprès d’un grand groupe sidérurgique. L’une de ses usines de production de fer blanc, acier sans étain et tôle noire, située en Europe, consommait d’importants volumes d’eau adoucie et osmosée, produits à partir de l’eau de ville et d’une eau de rivière. Nalco Water a mis en place un programme global de gestion de l’eau sur site. «Nous avons proposé une approche incluant la prévention des rejets de métaux lourds et l’amélioration du traitement des eaux usées grâce à une meilleure gestion et à la mise en place d’automatisme (technologie 3D TRASAR), ainsi que la conception, la construction, l’installation et l’exploitation d’une unité de traitement recyclant 160 m3 /h d’eaux usées dans le process. Dans le cadre d’un contrat de 10 ans, cette unité a permis d’économiser 1 million de m3 /an d’eau de ville et de réduire de 20% les eaux usées. L’industriel réalise ainsi une économie de 1,5 million d’euros par an» confirme Patrice Hervé (Nalco). Lenntech conçoit et met en place des filières complètes de recyclage, incluant, notamment, filtration sur média mixtes, ultrafiltration, charbon actif, résines échangeuses d’ions et osmose inverse en circuit fermé. Des installations de ce type sont utilisées, par exemple, pour recycler les eaux de TAR au Pays-Bas (2900 m3 /j) ou en Suisse (300 m3 /j) ou produire des eaux pour chaudière à vapeur à partir d’eau fortement saumâtre à Bahreïn (3600 m3 /j).
TMW
propose son Ecostill, un dispositif
d’évapo-concentration à basse température et pression atmosphérique,
capable d’utiliser une énergie fatale ou
de l’énergie solaire sur le site du client.
Ses modules d’évaporation en plastique
peuvent affronter les effluents les plus
corrosifs, issus du traitement de surface,
de la micro-électronique ou de procédés
salins. TMW en a par exemple installé
deux unités auprès d’un industriel de
la tannerie.
Chemdoc a pour sa part réalisé une
installation de production d’eau de process pour les unités d’électrolyse du site
de Kem One à Fos-sur-mer (Bouchesdu-Rhône), qui produit du chlore, de la
soude et de l’hydrogène. «Ils ont longuement étudié le choix entre une solution
membranaire ou des résines échangeuses d’ions. Finalement, étant habitués
à manipuler des produits chimiques et
produisant eux-mêmes les acides et bases
nécessaire à la régénération des résines,
ils ont choisi cette option. Nous avons
construit un système duplex pour produire 120 m3
/h d’eau déminéralisée à
partir de l’eau de la Crau, une eau brute
industrielle. Nous utilisons un procédé
avancé, dit cross flow, une combinaison de régénération à contre-courant
et de lits superposés de résine» détaille
Salvador Pérez (Chemdoc).
PASSER D’UNE SOURCE À L’AUTRE
Eau brute industrielle, eau de forage, eau de ville, eau recyclée: il arrive de plus en plus souvent qu’un même site industriel doive passer d’une ressource à une autre, notamment lors d’épisodes de restrictions de prélèvement. Or chacune de ces ressources exige en traitement particulier. Il faut donc soit multiplier les installations de traitement, soit concevoir des unités capables de s’adapter à différents types d’eau entrante pour produire la même qualité en sortie. Ce qui constitue un nouveau défi pour les traiteurs d’eau. «En traitement de surface, on n’arrive tout de même pas à recycler 100% de l’eau. Il faut toujours compenser les pertes. L’industriel opère donc avec de l’eau recyclée, très majoritairement, plus un complément d’eau brute traitée. Il demande donc une certaine flexibilité pour passer d’une ressource à l’autre, ou faire un mélange, et obtenir le même résultat à la sortie. Certaines technologies s’adaptent mieux à cette contrainte, en particulier les membranes» affirme ainsi Nabil Mabrouk (John Cockerill).
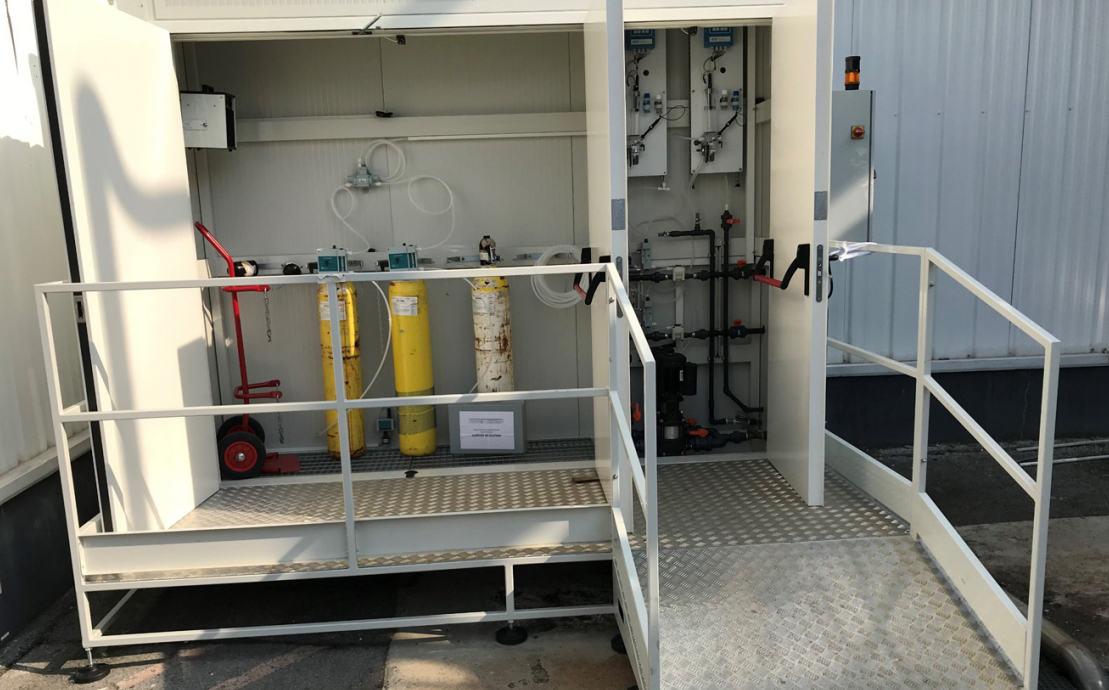
«En raison d’arbitrages liés au coût ou à la disponibilité des ressources, nous aurons à traiter des flux multiples. Il y a un champ de travail important pour adapter les membranes à cette variabilité et développer des systèmes agiles. Nous avons breveté le système Flexionic sur ce sujet. Il était à l’origine développé pour faire face aux variations de salinité d’eaux saumâtres mais, finalement, il trouve son intérêt et des applications en recyclage, avec des mélanges d’eaux conventionnelles et non conventionnelles. Il permet d’adapter le fonctionnement des membranes aux variations de turbidité, conductivité, charge organique etc. mesurées en ligne» précise Salvador Pérez (Chemdoc).
Le système a été appliqué,
en particulier, à l’usine Malvési d’Orano,
à Narbonne (Aude), un site de raffinage
de l’uranium. Le site utilise une eau souterraine provenant d’une résurgence,
ainsi que de l’eau pluviale (une obligation étant donné la nature de ses activités) et, occasionnellement, de l’eau de
ville et de l’eau usée traitée. «Nous avons
conçu un système Flexionic, intégralement membranaire pour produire de l’eau
pour la vapeur, la TAR et le process. Il
s’adapte seul à la qualité d’eau présente
dans cuve d’entrée (un mélange variable
de ces sources). Nous déployons actuellement le dernier volet, qui permettra de
recycler les eaux usées» révèle Salvador
Pérez.
TECHNOLOGIE : DES ÉVOLUTIONS PLUS QUE DES INNOVATIONS
Toutes les technologies de base sont matures, et il est aujourd’hui possible d’obtenir n’importe quelle qualité d’eau à partir de n’importe quelle source… à condition d’y mettre le prix. Cela n’empêche pas les évolutions. Ainsi, si l’osmose inverse est désormais courante (voir EIN 469), d’autres technologies membranaires naguère «de pointe» sont également devenues des procédés de routine. Ainsi des contacteurs membranaires qui permettent de dégazer l’eau, car on a souvent besoin de la débarrasser du dioxyde de carbone (CO2 ) ou du dioxygène (O2 ) dissous, ce qui se faisait classiquement par stripping ou chauffage. «Depuis quelques années, pour des raisons environnementales ou de sécurité des personnes, on se tourne vers les contacteurs membranaires. Nous utilisons une combinaison d’osmose inverse et de contacteurs membranaires dans notre procédé P-Gaz, pour produire à froid de l’eau déminéralisée et dégazée» explique Salvador Pérez (Chemdoc). EDF, par exemple, s’équipe de cette technologie pour maintenir la qualité de ses grands stockages d’eau déminéralisée et dégazée. «De même, l’affinage qui se faisait auparavant avec des lits de résines mélangés se fait maintenant avec l’électrodéionisation. Ce qui auparavant semblait coûteux et inutilement compliqué est aujourd’hui passé dans l’usage» ajoute-t-il.
NX Filtration propose pour sa part
une alternative à la combinaison classique ultrafiltration+osmose inverse.
Ses nouvelles membranes de nanofiltration à fibres creuses allient en
effet les capacités de rétention des
MES et pathogènes typiques de l’ultrafiltration à un seuil de coupure
de 400 ou 800 Daltons (de l’ordre
de la nanofiltration), qui permet de
retenir également les polluants organiques (DCO, DBO5, COT) et un grand
nombre de micropolluants (PFAS, etc.)
en une seule étape. «Nos membranes
offrent une alternative exceptionnelle
au couplage UF-OI, permettant des
économies d’énergie allant jusqu’à près
de 70% pour toutes les applications de
Réutilisation des Eaux Traitées (REUT)
ne nécessitant pas de déminéralisation»,
affirme Rémi Duvillard, Responsable
commercial France de NX Filtration.
Par ailleurs, et toujours sur la base des
technologies actuelles, l’accent est
de plus en plus mis sur des aspects
comme la nettoyabilité (pour des raisons d’hygiène en agroalimentaire) ou
la caractérisation en ligne de l’eau produite. «Le décret du 24 janvier s’intéresse
aussi à des aspects comme le stockage, la
validation avant distribution. Il faudra
aller au-delà des paramètres physicochimiques classiques et être capables de
mesurer la matière organique, la DCODBO, la charge bactérienne… Il existe déjà
des solutions, assez coûteuses. Il y a là
un vrai axe de développement» estime
Mikael Tournaux, de BWT.