Implanté en juin 2021 dans l'aire portuaire de Dunkerque, le site de retraitement des résidus chlorés IndaChlor doit traiter 40 000 tonnes d'effluents européens provenant principalement de l’industrie PVC. Pour une étape du procédé, le groupe Indaver a fait appel à Sodimate.
« Les effluents chlorés se présentent essentiellement comme des mélanges de solvants organiques liquides, inflammables et délicats à manipuler. L'incinération constitue le seul moyen de les traiter » explique Florian Rémy de l’entreprise belge Indaver, spécialisée dans la gestion durable des déchets. L'opération produit de l'énergie récupérable sous forme de vapeur et de l'acide chlorhydrique (HCl) qui est également valorisable auprès des industries chimique, pétrochimique et métallurgique.
La vente d’HCl aux concentrations standard (24% et 33%) suppose une légère modification du procédé, et une mise en citerne pour l’expédition. « Lorsqu’il n’y a pas de client pour l’acide chlorhydrique, nous devons le neutraliser par ajout d’une base avant de traiter le résultat et d’éliminer les déchets » poursuit Florian Rémy.
C’est ainsi pour la neutralisation qu’Indaver a fait appel à Sodimate sur la recommandation du fabricant de chaux, Lhoist. L'opération se déroule en deux étapes : d'abord avec l'apport de calcaire (carbonate de calcium CaCO3) en poudre pour faire remonter le pH de 0 à 3. Puis, avec l'ajout de lait de chaux pour atteindre la neutralité (pH 7). Suit un traitement par coagulation, floculation et décantation, une presse filtre pour déshydrater les boues et un traitement des gâteaux en filière spécialisée.
Deux contraintes, une solution
L'apport de carbonate de calcium dans le procédé d'Indaver répond à deux contraintes fortes : l'importante quantité de matière à apporter, le dosage précis des réactifs (HCl et CaCO3). « Nous consommons environ 150 tonnes par jour, soit le contenu d'un grand silo. Comme notre procédé fonctionne en continu, il nous fallait un double silo pour pouvoir passer le week-end sans livraison de CaCO3 » justifie Florian Rémy.
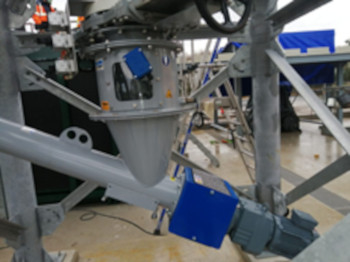
Atout maître du dispositif proposé par Sodimate, l’ensemble dévoûteur-doseur breveté. L’entreprise s’est ainsi vue confiée la conception, la construction et l’installation du matériel assorti du dispositif d'inspection et de sécurité nécessaires.
L’installation, pourvue d'un revêtement spécifique pour résister à l'atmosphère corrosive du bord de mer, comprend :
- deux silos en polyester de 100 m3, soit 150 tonnes de calcaire par silo. Chaque silo est muni d'un cône de sortie, d’un dévoûteur mécanique DS 400 et de percuteurs pneumatiques pour faire descendre le calcaire lorsque le silo est presque vide, ainsi que de soupapes de sécurité, pressostats, détecteurs de niveau à palettes, contrôleurs de rotation, détecteurs de bourrage, système de pesage, etc.
- chaque dévoûteur fonctionne de concert avec une vis de dosage rigide VRT 168 (diamètre 168 mm). Particulièrement robuste, le doseur est calibré pour fournir de 2 à 8 tonnes de CaCO3 par heure. Le débit est ajusté par un variateur de fréquence agissant sur le moteur du doseur. Il dépend de manière linéaire de la quantité d'acide envoyée dans le réacteur, puisque les deux réactifs doivent être présents en proportions stœchiométriques. « On affine la régulation par une boucle d'asservissement commandée par une sonde de pH placée dans le réacteur, car la qualité du calcaire peut varier d'une livraison à l'autre »,
- les deux vis doseuses convergent vers un unique convoyeur (diamètre 219 mm) alimentant le bassin de réaction de 30 m3. Il peut être fermé à l'embouchure par une vanne guillotine motorisée,
- les réservoirs sont rechargés par une noria de camions. Chacun est muni d'un détecteur signalant la présence (ou non) d'un camion au contact du silo. Un filtre pneumatique, qui ne fonctionne que durant le dépotage du produit dans le silo, assure le dépoussiérage de l'air rejeté. Les cartouches filtrantes sont ensuite décolmatées par injection d'air frais,
- chaque silo est pourvu en partie basse d'une vanne à registre bloquant totalement l'écoulement. Elle se ferme lors des opérations de maintenance ou de réparation, ce qui permet d'intervenir sans devoir vider le réservoir.
Quatre mois ont suffi à Sodimate pour construire, tester et installer
l'équipement. L'usine IndaChlor, dont Indaver revendique le modèle d’économie
circulaire, est opérationnelle depuis juin 2021.