Malgré les gros efforts engagés par les industriels pour réduire les consommations d’eau et réutiliser ou recycler tout ou partie des eaux utilisées, le secteur agroalimentaire reste un gros consommateur d’eau. En amont, les industriels sont contraints d’engager des traitements poussés de leurs eaux de process pour les besoins variés de leur production. En aval, ils doivent traiter une grande quantité d’effluents souvent chargés en pollution organique et en graisses. Des procédés se développent qui permettent d’économiser l’eau tout en valorisant les effluents ainsi que certains sous-produits. L’objectif est partout le même.: diminuer l’empreinte eau, conformément à la norme ISO 14046 qui propose un cadre et des lignes directrices pour l’évaluation de l’empreinte eau des produits, procédés et organisations.
Dans les industries agro-alimentaires, les sources et usages de l’eau sont multiples. Certaines eaux n’entrent pas en contact avec le process alimentaire, ce sont les eaux dites d’utilités industrielles dont l’origine est variable : eaux de ville, de forage, issue d’un système de recyclage, etc. Elles vont servir pour le lavage, le refroidissement dans les circuits aéroréfrigérants, le convoyage, etc.
Mais bien sûr de l’eau y est aussi utilisée pour le process agroalimentaire, ce n’est pas qu’un banal fluide. Elle peut ainsi entrer en contact direct avec les denrées alimentaires produites, voire même en constituer un des ingrédients à part entière sous forme liquide, de glace ou de vapeur. Exemple emblématique.: l’eau utilisée comme véritable matière première par les fabricants de boissons et autres sodas : les “embouteilleurs”.
Des électrodes de diamant pour désinfecter les eaux de lavage de fruits et légumes
La qualité des eaux de nettoyage des fruits et légumes peut conditionner fortement celle des produits, leur aspect et leur goût, ainsi que leur durée de conservation.
Les unités automatisées Agrineo™ substituent aux traitements chimiques, le procédé DiaClean® qui repose sur des électrodes en diamant artificiel pour désinfecter les eaux sans produit chimique et sans laisser de résidus sur les fruits ou dans les jus.
La technologie DiaClean® produit des oxydants puissants directement dans l’eau des cuves, permettant à celle-ci de jouer pleinement et de façon continue son rôle de media désinfectant au service des fruits et légumes.
Développée par Waterdiam, la technologie DiaClean® permet d’inactiver les espèces microbiologiques, bactéries et champignons, abat les polluants organiques et réduit la DCO sur les eaux de traitement après récolte. Elle permet de respecter les normes alimentaires tout en réalisant des économies d’eau et de maintenance, en minimisant, voire éliminant, les besoins en produits formulés ainsi que les arrêts de ligne pour nettoyage ou renouvellement d’eau.
Malgré les efforts engagés par les industriels pour réduire les consommations et réutiliser ou recycler tout ou partie des eaux utilisées, le secteur agroalimentaire reste donc, de par la nature même de ses activités, un gros consommateur d’eau dont il faut absolument assurer et garantir la qualité… tout en l’économisant.
Chez les embouteilleurs, ce dernier critère est d’ailleurs de plus en plus prégnant : « les standards de production adoptés par les grands groupes imposent des objectifs de ratio d’embouteillage, confirme Philippe Onillon, Responsable Commercial de zone et Marketing chez I.C.E. Dans le segment d’activité des Carbonated Soft Drinks (CSD), des ratios couramment situés autour de deux litres d’eau brute par litre produit doivent être réduits à 1,4 hors nettoyage ». Une évolution dictée par plusieurs facteurs qui varient selon les différentes régions du monde.: raréfaction des ressources en eau, réglementations restrictives sur les ressources ou sur les usages, marketing « vert… sans oublier la nécessité produire constamment plus avec des ressources identiques ou contraintes ».
Économiser l’eau : une préoccupation constante
Cette course à l’économie d’eau touche l’ensemble des secteurs agroalimentaires.
Les industriels se tournent donc de plus en plus souvent vers des systèmes leur permettant de connaître en temps réel et le plus finement possible leurs consommations d’eau dans leurs usines. Pour satisfaire ce besoin, BWT a par exemple lancé une solution nommée “Vision™”. Elle repose sur une box qui récupère une foule d’indicateurs sur les consommations d’eaux de l’industriel via des capteurs disséminés sur l’ensemble des points de consommation.
Une fois traitées et interprétées, les données sont accessibles via tablette, ordinateur ou Smartphone. Un acheteur, un responsable d’ingénierie, un ingénieur process, peut ainsi savoir, à tout moment, ce que consomme en eau chaque kilo de produit sur les différentes chaînes de ses usines. Des alertes se déclenchent en cas de franchissement de seuils critiques.
De son côté, GE a développé depuis 2010 la solution Insight™ qui, en plus de récupérer les signaux de capteurs, permet également la gestion analytique, documentaire et le diagnostic à distance des systèmes de traitement d’eau. Insight repose sur les compétences du groupe GE et de sa filiale GE Digital.
.jpg)
De même, la technologie 3D Trasar de Nalco permet de réduire les consommations d’eau en optimisant les installations existantes, de réutiliser les eaux quand c’est possible, voire de les recycler en mettant en place des prétraitements avant recyclage. L’objectif final étant toujours de minimiser les consommations d’eau tout en maximisant les résultats et en optimisant les coûts opératoires.
.jpg)
Ses applications centralisées dopent les besoins en instrumentation et systèmes d’analyse. Endress+Hauser a ainsi développé et adapté son instrumentation aux exigences particulières des industries agroalimentaires. Mesure de niveau sans contact pour poudres ou liquides pour piloter de façon optimale la production et les approvisionnements, mesure de pression hydrostatique, mesure et surveillance de température débitmétrie massique et électromagnétique, viscosimètre…
Les applications sont très nombreuses et reposent également sur un suivi analytique sans faille. Beaucoup de sites de production disposent par exemple d’un process de nettoyage en place utilisant des produits acides (acide nitrique) ou alcalins (soude).
La conductivité est alors le principal paramètre permettant de surveiller et de réguler la concentration des agents de nettoyage. Elle permet de gérer la séparation entre l’eau de pousse et le produit noble (ex..: lait…) mais aussi la séparation entre l’eau et les produits de nettoyage lors de leur retour vers l’installation. Pour ce type d’application, Endress+Hauser a développé un conductivimètre inductif compact, le Smartec CLD18 dont la compacité facilite l’intégration, notamment sur les skids. Le Smartec CLD18 optimise le process grâce à des mesures rapides et fia-bles pour la séparation de phases et la surveillance de la concentration des produits de nettoyage. Sa construction hygiénique protège les produits de la contamination.
.jpg)
La réduction des pertes matières est également un enjeu majeur en agroalimentaire, notamment dans les industries de transformation du lait. Les objectifs sont partout les mêmes.: limiter la perte de produits durant le processus de fabrication, réduire la charge polluante et valoriser les sous-produits. OUSAF11, un capteur optique capable de détecter les pertes de lait ou de crème dans le canal de rejet de l’usine, répond à ce type de besoins. Il peut bien sûr s’intégrer dans une installation complète associant, par exemple, une mesure de débit, une télétransmission, une caméra visualisant l’effluent, un préleveur d’échantillon et d’autres paramètres comme le pH ou la conductivité.
Les économies passent aussi par un suivi analytique en continu des différentes qualités d’eau utilisées.
.jpg)
Chez Krohne, l’Optiquad permet une mesure précise, directe, et en ligne de la DCO, très utilisée en laiteries et fromageries pour la mesure de la teneur en acide gras libres, en matière grasse, en protéines… (voir encadré).
Par ailleurs, le rapport DCO/COT apporte par exemple des informations importantes sur certaines liaisons organiques (alcools, protéines, etc.).
Les analyseurs de COT développés par Shimadzu, Hach-Lange, Metrohm, Datalink ou encore Endress+Hauser s’attachent à améliorer le rendement des process en réduisant les coûts au quotidien.
« On rencontre des composés organiques dans presque tous les types d’eau, depuis l’eau potable en passant par l’eau de process et de refroidissement, jusqu’à l’eau destinée à l’usage pharmaceutique et à la production de produits alimentaires, explique Pierre Guillou chez Metrohm. La détection précoce des contaminants organiques est d’une grande importance dans la protection des installations industrielles et de l’environnement. Le COT est un paramètre global, qui est parfaitement adapté pour le suivi 24-24 et 7 jours sur 7 (charge totale de polluants) ».
.jpg)
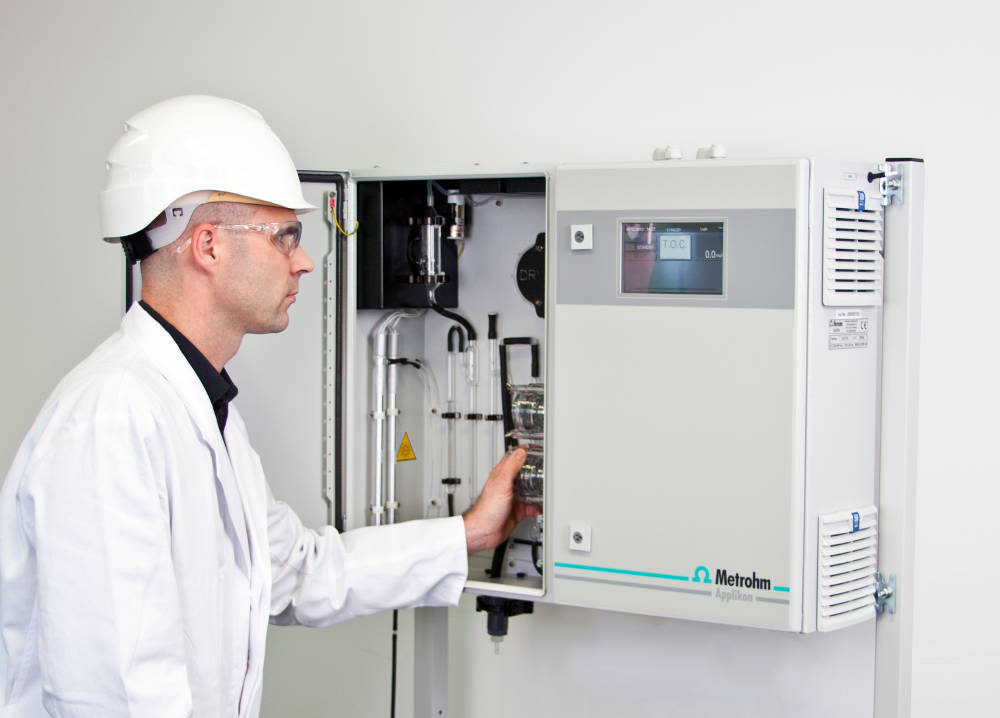
Ainsi, COT-mètre “Sievers®” de GE est capable de mesurer la matière organique en sortie de rinçage… toutes les quatre secondes. « La performance du Sievers permet ainsi de stopper plus vite le rinçage dès que la charge en matière organique est redevenue acceptable, et ainsi d’économiser davantage d’eau », indique Fabienne Tissandier, responsable Instrumentation chez GE.
.jpg)
Certains produits chimiques, les fameux produits formulés, utilisés en agroalimentaire permettent aussi d’optimiser la consommation d’eau, d’énergie et de matières premières.: antitartres, inhibiteurs de corrosion, produits anti-dépôts pour éviter l’encrassement des évaporateurs, etc. De gros acteurs s’investissent dans ce type d’offre comme par exemple Nalco ou BWT qui vient de lancer Aqaster™, une offre packagée destinée au marché de la conserverie et de l’embouteillage. Formulé spécifiquement pour les applications de stérilisation et pasteurisation, Aquaster™ permet de minimiser substantiellement les taux de rebuts. De même avec “Food Pro”, GE Water & Process Technologies développe une gamme spécifiquement dédiée au secteur agroalimentaire.
Filtrations en cascade
Au-delà des économies d’eau, l’un des gros enjeux pour les industriels de l’agroalimentaire reste l’obtention d’une eau de qualité constante pour leurs process. De nombreux équipements permettent d’y parvenir, à commencer par les systèmes de dégrillage fin tels que les filtres autonettoyants à disque mécanique “Hydrotech Discfilters” ou à tambour mécanique (Hydrotech Drumfilters) de OTV DBI (Veolia Water STI) ou les dégrilleurs in line de Tecnofil.
Ces deux acteurs développent également des process de clarification pour supprimer les particules en suspension : clarificateur particulaire fonctionnant sur le principe de la floculation lestée associée à la décantation lamellaire à contre-courant chez OTV DBI, clarificateur particulaire fonctionnant sur le principe de la décantation lamellaire à contre-courant chez Tecnofil (Decantec-Néo), etc. « Les particules en suspension, notamment sous forme colloïdale peuvent s’avérer très problématiques pour la rentabilité, lance Olivier Tognetti, Responsable de la zone Asie-Pacifique chez I.C.E. Dans le cas d’une unité d’embouteillage par exemple, elles peuvent encrasser tous les systèmes de filtration. À la clef : une hausse des coûts de fonctionnement et des dérives sur les systèmes d’éliminations sélectifs ».
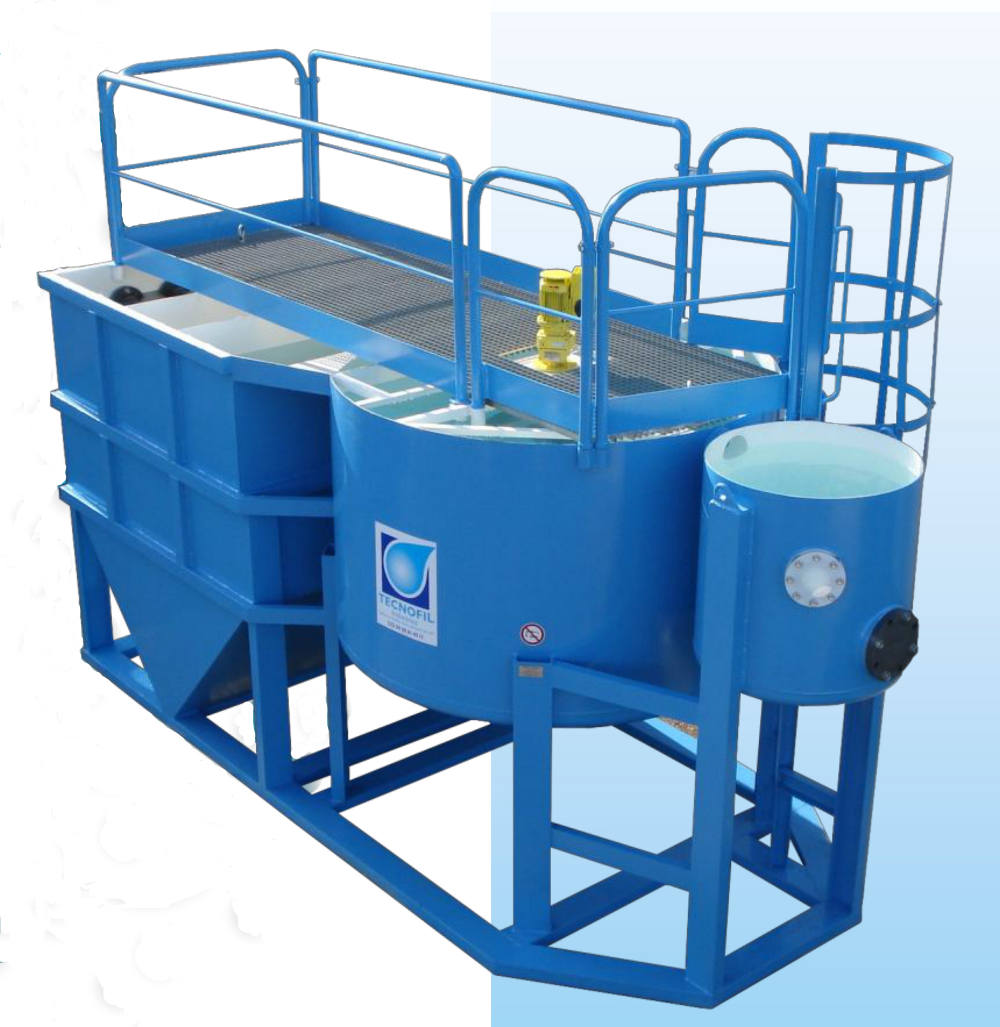
Pour maîtriser la contamination microbienne et particulaire, les industriels de l’agroalimentaire recourent de plus en plus souvent à la filtration sur cartouches qui permette de produire une eau de process exempte de matières en suspension, colloïdes, virus, bactéries, endotoxines…
Le panel s’étend de la filtration sur media filtrant granulaire à l’ultrafiltration par membrane céramique, cette dernière technique éliminant la totalité des pollutions particulaires. « Nous notons un recours croissant à ce type de procédé, que ce soit sur membranes organiques ou minérales, car il satisfait aux exigences croissantes d’économies d’eau, d’énergie et de consommables tout en ayant une grande flexibilité quant aux variations de la qualité de l’eau brute », confirme Patrick Ballato, Directeur Innovation et Développement chez I.C.E. Pas de consommable et peu de maintenance, les filtres aident les industriels à réduire leurs coûts d’exploitation.
L’offre est très large, portée par Pall, Eaton, Scam-Filtres, Eurofiltres, Ocène, GE distribué en France par Elma Technologies, OTV DBI avec ses systèmes d’ultrafiltration “Uflex”, BWT qui propose des filtres d’adoucissement et ultrafiltration sur mesure, ou encore Tecnofil avec des filtres à charbon actif et filtres multimédia vertical à plancher. Chez GE, l’offre se compose de trois grands types de cartouches filtrantes : Z.Plex® (filtration en profondeur, en fibre de propylène thermo-soudées pour filtration nominale ou absolue), Flotrex® (cartouches plissées avec média filtrant de microfibres pour filtration nominale ou absolue) et Memtrex® (cartouches plissées avec média filtrant membranaire pour filtration absolue de 1 à 0.03 micron).
Dans l’industrie de la boisson, toute l’eau entrant en contact avec le produit ou son contenant, peut ainsi être préalablement stérilisée par filtration absolue à 0,2 micron avec des cartouches Memtrex®. Sur certains process, des filtres peuvent être eux-mêmes protégés par d’autres filtres selon le principe de la filtration en cascade.
Réutiliser les eaux de vache pour réduire l’empreinte eau
Dans l’industrie laitière, grâce à son expertise reconnue des eaux de process, SUEZ accompagne ses clients en leur proposant des solutions pour réutiliser leurs évaporats et réaliser ainsi de fortes économies d’eau. En fonction de la qualité d’eau souhaitée pour les différentes applications du site, les évaporats peuvent ainsi être réutilisés en chaufferie, sur les tours de refroidissement ou encore en nettoyage.
Dans ce cadre, SUEZ a développé des produits dispersants et passivants, issus de la gamme aqualead®, afin de rendre les «.eaux de vache.» utilisables en chaudière vapeur. En effet, cette utilisation particulière nécessite la mise en place d’un programme de traitement chimique spécifique et rigoureux en chaudières, afin d’empêcher leur encrassement dû à la forte charge organique des évaporats.
Pour valider les possibilités de réutilisation des eaux de vache, SUEZ établit en premier lieu un diagnostic complet des consommations d’eau du site et du bilan financier qui en découle.: quantité d’eau de ville utilisée, quantité d’évaporats produits, besoins en eau des différentes applications et volumes des rejets annuels. Ensuite, une campagne d’analyses des évaporats est effectuée, afin de déterminer avec précision leurs niveaux de qualité et de proposer les solutions optimales pour les réutiliser.
À titre d’exemple, dans une laiterie produisant de la caséine et de la poudre de lactosérum, près de 100.% des évaporats ont pu être réutilisés en appoint des chaudières vapeur, en réduisant d’autant la quantité d’eau de ville précédemment utilisée. Sur ce site, près de 90.000.m3/an d’eau de ville sont ainsi économisés chaque année. De plus, les évaporats étant faiblement minéralisés, les purges ont été également réduites. Au total, les économies engendrées par l’utilisation des évaporats en alimentation des chaudières sont estimées à 140.000.€/an sur ce site.
L'essor de l'osmose inverse
Hytec, Firmus, Corelec, GE, Actibio, BWT, TIA, Suez, OTV DBI, I.C.E... de plus en plus d’acteurs du traitement de l’eau travaillent sur des systèmes d’osmose inverse. Ils reposent sur l’utilisation de membranes semi-sélectives permettant ou favorisant certains transferts de matières par rapport à deux milieux qu’elles séparent.
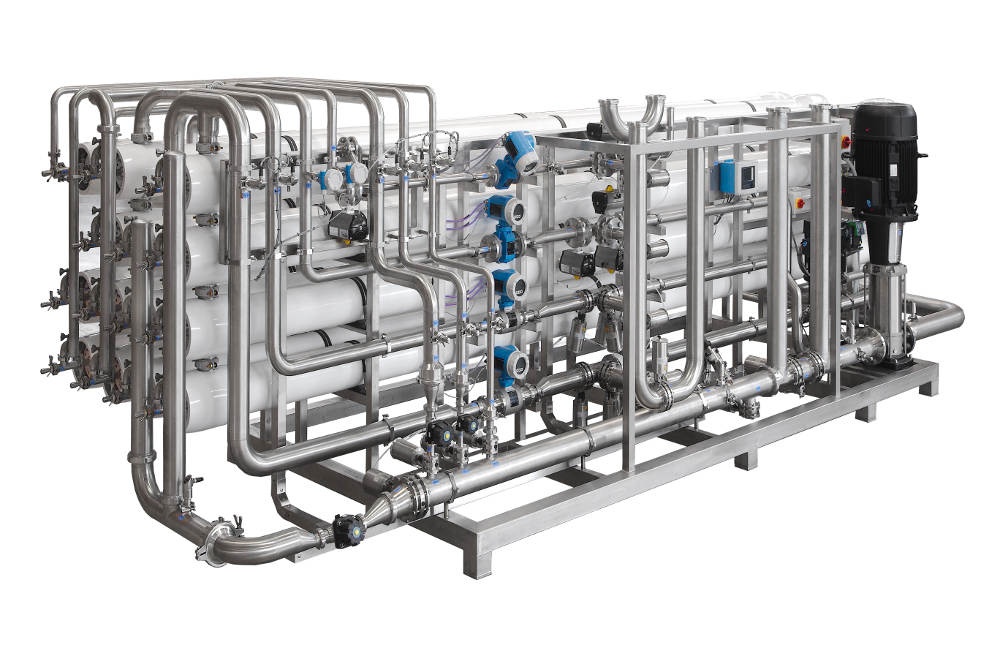
Elles permettent de retenir à la fois les ions monovalents et les ions bivalents. Ces systèmes peuvent être utilisés seuls ou en combinaison avec d’autres process comme par exemple l’échange d’ions. Les membranes présentent l’avantage d’éliminer 99 % des composés inorganiques et organiques tels que les colloïdes et des particules.
En Algérie, Hytec a récemment installé trois lignes d’osmose inverse de 84 m3/h unitaire et trois lignes d’ultrafiltration de 125 m3/h unitaire pour la production d’eau déminéralisée à partir d’eau de forage pour la fabrication de jus de fruits. « Le stockage des concentrats d’osmose sert de réserve incendie et l’eau est réutilisée pour le lavage des routes et de l’usine et à des fins d’irrigation », précise Laurent Larcher, Directeur commercial chez Hytec.
Chez I.C.E., qui développe des unités d’osmose inverse à très haut taux de conversion depuis plusieurs années, on souligne également cette tendance. « Nos clients veulent maîtriser leurs coûts de production en intégrant l’économie d’énergie, en intégrant des systèmes retro-lavables afin de limiter le coût de remplacement de cartouche de filtration single use (procédé type micro et Ultrafiltration membranaire) », indique Olivier Tognetti. C’est ainsi qu’au Pakistan, I.C.E. a réalisé une unité d’osmose inverse à 83.% de conversion sur la base d’une eau dont la teneur en sels dissous est à 12.g/l, soit la moitié de l’eau de mer et sur laquelle la société a intégré un récupérateur d’énergie pour réduire la consommation électrique.
.jpg)
Lorsque l’on vise une réduction de la minéralisation au sens large, ou encore lorsque les médias spécifiques ne sont pas exploitables, l’osmose inverse permet de réduire d’un facteur 10 à 50 la plupart des composés dissous. I.C.E. adapte à chaque cas d’application un étagement sur mesure d’osmose, en privilégiant la nettoyabilité des systèmes, le rendement hydraulique (jusque 95.%) et la sélection de membranes travaillant à moindre pression, donc moins énergivores.
BWT met également souvent en œuvre des systèmes d’osmose inverse sur mesure. « Avec, on produit par exemple de l’eau osmosée pour alimenter des générateurs de vapeur afin d’obtenir une eau de basse conductivité à faible teneur en sels minéraux, indique Raphaël Gallais, Directeur de Marché Industrie et Directeur des Ventes Internationales chez BWT France. À la clef : moins besoin de purger, moins d’appoints en eau et de produits formulés… et au final, une consommation d’eau optimisée et un rendement énergétique maximisé. «.Aujourd’hui le taux de conversion des osmoseurs peut atteindre 85 à 90.%.», ajoute-t-il.
Les techniques membranaires trouvent également un nombre croissant d’applications en eaux usées (traitement d’affinage) pour rejet ou réutilisation.
.jpg)
Eaux usées : la valorisation plébiscitée
Un abattoir a ainsi sollicité GE pour équiper sa nouvelle installation de traitement d’effluents par la technologie BRM (Bio Réacteur Membranaire) avec les membranes UF Zeeweed®. Le débit à traiter était de 9.500 m3/semaine avec une charge de 18.000.kg/semaine de DCO. Après traitement dans le bioréacteur équipé de ces membranes, la DCO en sortie de station était inférieure à 30.mg/l et la MES inférieure à 2 mg/l. Aujourd’hui, l’eau traitée est presque intégralement recyclée, notamment grâce à un traitement par osmose inverse, et permet de diminuer significativement ses coûts d’exploitation.
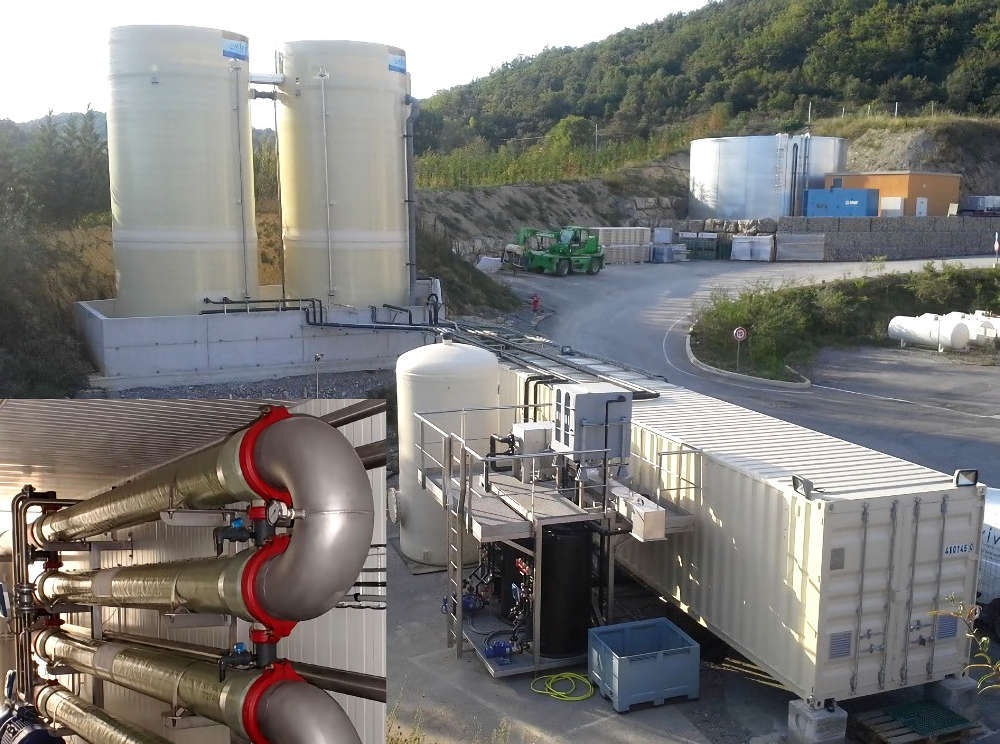
Autre exemple dans une grande coopérative laitière recevant plus de 2000 t de lait chaque jour chargé à 87.% d’eau qui a opté pour les membranes GE Duratherm™ pour purifier les condensats d’évaporation par osmose inverse. Objectif.: réutiliser les 1.800.t/j de perméat ainsi généré (alimentation en chaudière, nettoyage à chaud…). Les économies réalisées vont bien au-delà des économies en eau, les volumes réutilisés n’étant pas dirigés vers la station de traitement des effluents ; une économie substantielle est aussi réalisée sur les produits chimiques et l’énergie nécessaires aux traitements des eaux usées. Enfin, la chaleur conservée et valorisée représente un montant d’économie comparable, grâce à une alimentation partielle de la chaudière à 65.°C. Le retour sur investissement de cette installation a été évalué à neuf mois par une agence indépendante.
Pour réduire les arrêts nécessaires aux lavages des membranes et par conséquent la consommation de réactifs chimiques, OTV DBI a développé de son côté le BiopROtector® qui élimine biologiquement la partie organique des effluents, des condensats, des eaux de vache avant UF/RO.
À l’aval des process alimentaires, il se dégage deux catégories d’industriels. Ceux qui rejettent leurs effluents au réseau après prétraitements, n’ont pas toujours intérêt à rechercher des économies d’eau car ils dépassent déjà souvent les limites réglementaires en DCO et leur consommation journalière est souvent inférieure à 100.m3/jour. « Mais cette situation est généralement acceptée par le gestionnaire du réseau car leurs effluents sont facilement biodégradables et d’autant plus que nombre de stations urbaines sont en sous charge », comme le remarque Laurent Larcher chez Hytec.
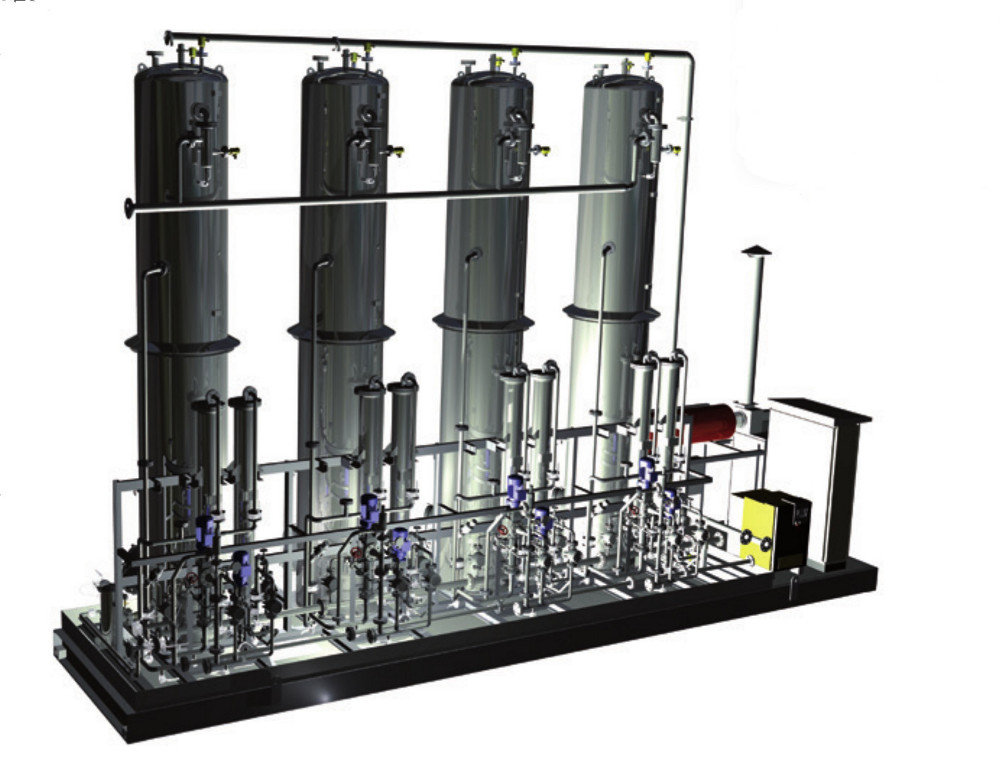
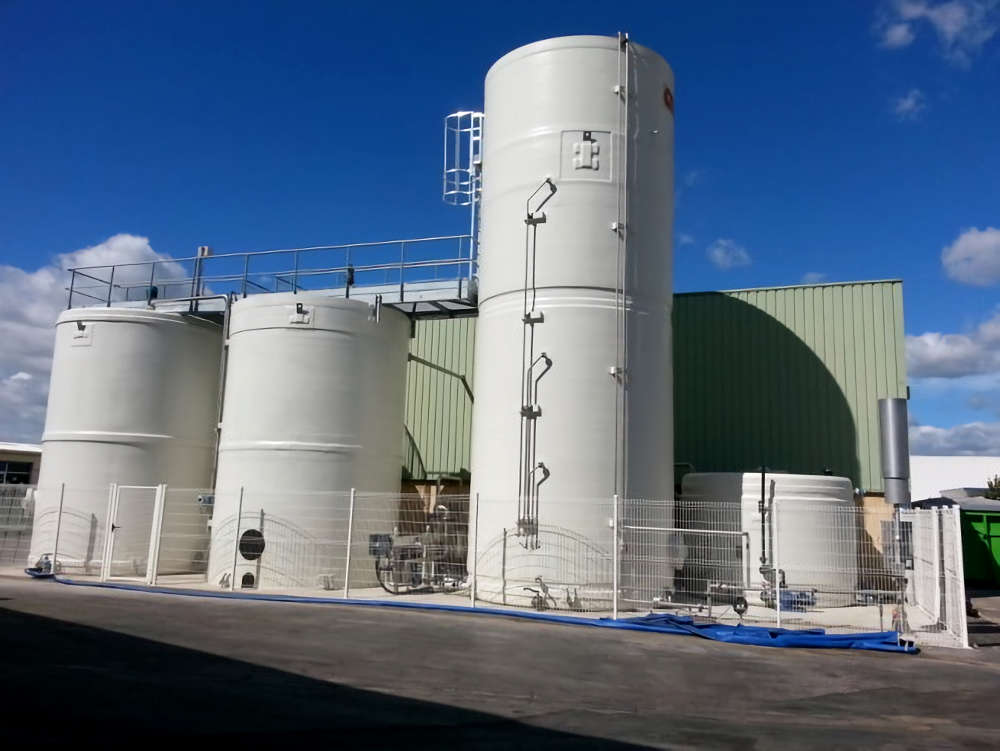
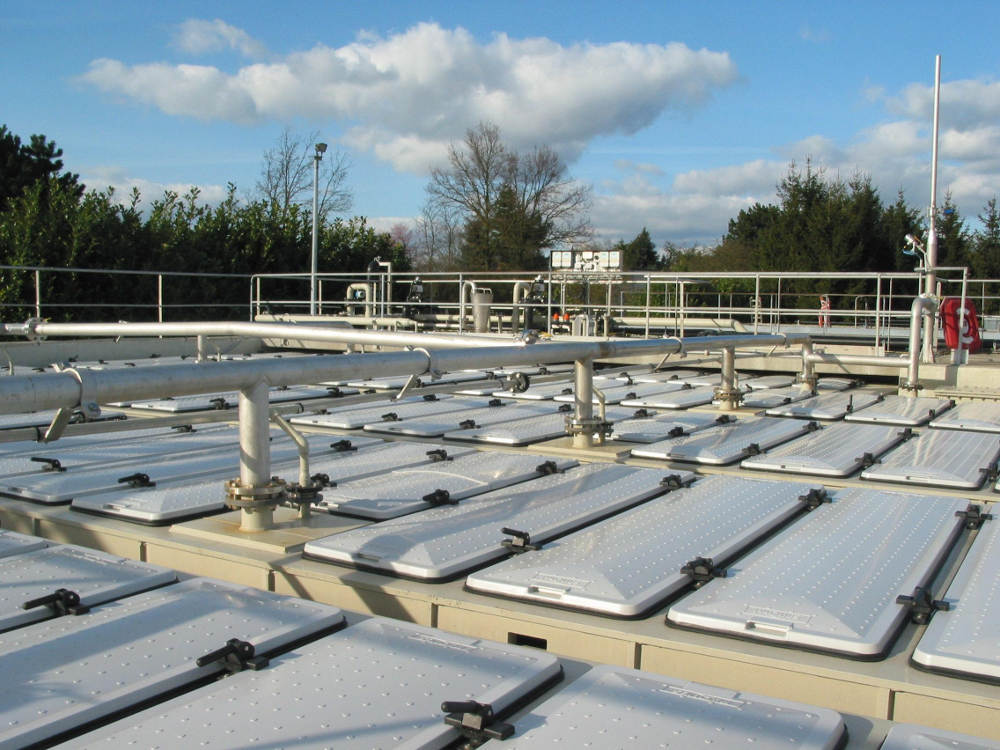
Ceux qui rejettent au milieu naturel, notamment en raison d’un volume d’effluents trop important, doivent mettre en place des traitements performants. « Pour réduire les investissements et les coûts d’exploitation, ils ont intérêt à économiser l’eau, comme par exemple Materne qui est passé de 7 litres à 3,5 litres pour traiter un kilogramme de pommes ». Materne a en effet fait appel à Hytec pour traiter les effluents d’une de ses usines spécialisées dans la production de compotes et confitures à Boué.
L’installation mise en place repose sur un méthaniseur granulaire vertical à recirculation de 20.m3/h, six réacteurs biologiques aérobies à biomasse fixée immergée, un traitement physico-chimique avec aéroflottateur pour la séparation de la biomasse en excès et une unité de déshydratation des boues par centrifugation. « Les effluents sont rejetés au milieu naturel avec une valeur en DCO inférieure à 90.mg d’O2/l pour une DCO initiale supérieure à 6.000.mg, précise Laurent Larcher. La production de boues et la consommation d’électricité y sont très faibles, le biogaz est valorisé pour réchauffer les effluents et les échangeurs de chaleur sont peu sensibles à l’encrassement ».
Valorisation énergétique des effluents, recyclage, méthanisation et réduction des boues figurent parmi les solutions plébiscitées par les industriels du secteur. Les traitements les plus couramment mis en œuvre découlent de ces préoccupations.
« Les effluents agro-alimentaires se caractérisent généralement par des charges organiques importantes », précise-t-on chez Ovive. Mesurées par la DCO et la DBO5, elles sont traitables selon qu’elles soient solubles ou particulaires. La DCO particulaire peut être traitée par voie physico-chimique et séparation physique par flottation ou décantation. La DCO soluble ou dissoute est traitable par voie biologique. Il convient de réaliser une phase d’étude (pilotes laboratoires ou sur site) avant de se lancer dans un dimensionnement de station de traitement. Vendus sous la marque Biomembrat, les réacteurs biologiques membranaires présentent les avantages d’une production de boues moindre par rapport aux procédés de boues activées classiques et de pouvoir réutiliser l’eau traitée sur l’usine.
La méthanisation, initialement développée pour traiter les effluents fortement chargés en matières organiques (à partir de 10.kg/DCO/m3 jusqu’à 50.kg/DCO/m3), des industries agroalimentaires continue à progresser en volume.
L’Ozone au service de la sécurité alimentaire
Connu pour son action désinfectante, l’Ozone s’est imposé comme une réponse sûre et efficace et comme une alternative à la surutilisation des produits chimiques.
Les générateurs ozonia® TOGC développés par SUEZ sont des unités de production d’ozone spécialement conçues pour les applications industrielles. L’ozone est utilisé pour le rinçage des bouteilles, des contenants ou appareils de production pour éviter la contamination par des germes. Cette application de l’Ozone permet ainsi d’améliorer la sécurité alimentaire, tout en diminuant les rejets polluants. Cette solution permet même de supprimer l’utilisation de produits chimiques rémanents.
Seule ou associée à un traitement aérobie, elle est portée par des acteurs tels que Suez, OTV DBI, Enprotech, CMI Proserpol, Biome, Atlantique Industrie, Ovive ou encore Aeroe et permet de réduire le volume des boues tout en produisant une partie de l’énergie nécessaire au fonctionnement des process.
Très rentable du point de vue efficacité, la technologie UASB et ses variantes ont fait leurs preuves sur les grandes installations.
Des équipements de plus faibles capacités, se sont développés en parallèle grâce à par des acteurs comme Naskeo Environnement, ou Aqua Corp. et son partenaire belge Enprotech, et trouvent désormais de larges débouchés sur le marché.
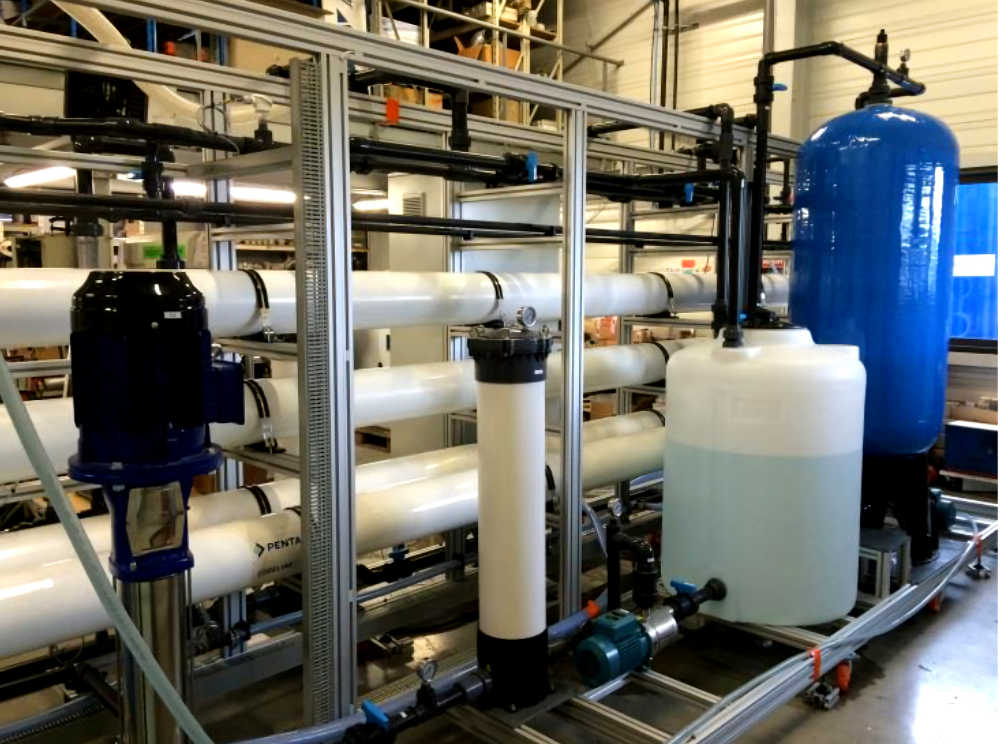
Aquacorp avec le réacteur anaérobie “BioActor” traite par exemple les eaux usées chez le producteur de légumes Greenyard Foods. L’Européenne d’Embouteillage, filiale du groupe Groupe Orangina Schweppes France installée à Meyzieu (69), a décidé de son côté de mettre en service une installation de méthanisation de ses effluents industriels reposant sur la technique du lit de boues granulaires et un séparateur triphasique (EGSB).
C’est OTV DBI qui a été chargé d’installer cette filière : système de neutralisation, traitement anaérobie Biobed et valorisation du biogaz (chaudière biogaz). Résultat : l’embouteilleur a réduit les boues et gagné en autonomie thermique.
L’installation lui permet par ailleurs une meilleure acceptabilité environnementale avec le traitement des odeurs et une très faible nuisance auditive.
OTV DBI propose également sa gamme standardisée Thanium de méthaniseurs de petites tailles.
De la glace pour réduire la consommation d’eau
Avec Ice Pigging, SUEZ offre à l’industrie agroalimentaire une solution pour améliorer significativement ses procédés de nettoyage en place. Cette technologie propose de remplacer l’injection d’eau pour le nettoyage des tuyaux sur les lignes de production par un bouchon de glace.
La glace s’adapte aux courbes et aux changements de diamètre des canalisations. Elle permet de les nettoyer en profondeur, tout en récupérant du produit qui aurait été perdu avec une technique de nettoyage classique. Pour certains produits comme par exemple la mayonnaise ou la confiture, c’est même la seule façon de nettoyer efficacement les tuyaux avant d’y faire passer un autre produit.
En remplaçant l’injection de grande quantité d’eau par un bouchon de glace, Ice Pigging permet de réduire la consommation d’eau, réduire la quantité d’effluents produits et de réduire les temps de nettoyage des machines.
Des tests réalisés au Royaume-Uni ont montré que l’utilisation d’Ice Pigging permettant d’augmenter les revenus d’environ 410.000.€ par an grâce aux quantités de produit récupéré et à la réduction de la durée des interruptions de production.
Ice Pigging a reçu le prix de la Meilleure Innovation Fabrication/Transformation Alimentaires 2016 lors des Trophées mondiaux de l’Innovation Alimentaire (World Food Innovation Award).
La valorisation de certains sous-produits se développe également fortement. Alcion Environnement propose ainsi ses procédés de valorisation d’ammoniac “Valeaz” et de CO2.: Valecarb. « Ce dernier intéresse les industriels de l’agroalimentaire qui réalisent des fermentations et/ou digestions pour produire du biogaz et de l’alcool, indique Jean-Philippe Ricard, le Directeur. Nous valorisons du CO2 sous forme de bicarbonate de soude qui peut être utilisé dans le traitement de l’air, l’agroalimentaire et les cosmétiques ».
De même, très Impliqué dans le développement des énergies renouvelables, OTV DBI propose la méthanisation d’effluents très chargés (Lactosérum, vinasses…) avec son Memthane® - méthanisation asssociée à une séparation membranaire - ou de déchets solides avec son Biomet®, avec un objectif de production de biogaz, utilisé in situ, ou de biométhane réinjectable. « Tous les projets que nous étudions en eau de process ou en effluents industriels, sont marqués par la volonté de recycler l’eau, économiser l’énergie, réutiliser les sous-produits, autant de facteurs qui signent durablement l’engagement et la responsabilité d’un professionnel emblématique de l’Environnement », souligne Thierry Legube, Directeur commercial.
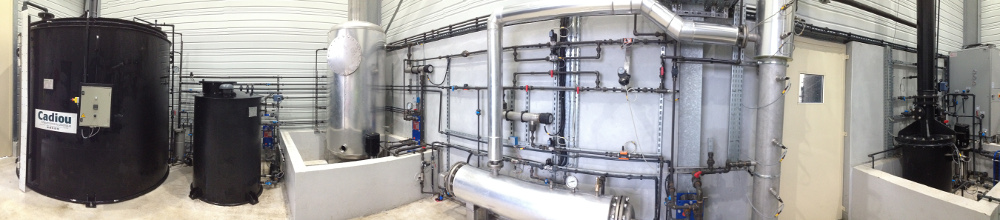